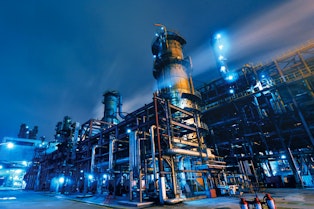
Electrification has its limits. Electric vehicles can replace internal combustion engine cars; solar, wind and other renewables, plus energy storage, can outperform oil, gas and coal power on the grid. But for many industries, going electric is not really an option.
This includes some forms of transport. Most obviously aviation, but also shipping and heavy goods transportation, all lack a clear, currently actionable route to electrification.
Instead, low-carbon hydrogen–either used in fuel cells or synthetic carbon-neutral fuels—are in the crosshairs as potential replacements for fossil fuel. And hydrogen could also tackle an even more serious challenge to decarbonization.
According to the Brookings Institution, “Steel, cement and chemicals are the top three emitting industries and are among the most difficult to decarbonize.”
These essential industries account for around 16% of global carbon emissions, so finding ways to decarbonize them is a priority if we are to head off a climate crisis.
The challenge facing these industries is down to technical factors such as the need for high heat and process emissions of carbon dioxide, and economic factors including low profit margins, capital intensity, long asset life and trade exposure, Brookings says.
These essential industries account for around 16% of global carbon emissions, so finding ways to decarbonize them is a priority if we are to head off a climate crisis. And each one has different pathways to decarbonization.
Decarbonizing steel
According to the World Steel Association, every ton of steel produced in 2018 emitted on average 1.85 tons of carbon dioxide.
The carbon in question is not just produced through the energy demands of the processes that convert iron ore into useable steel; the process itself generates emissions.
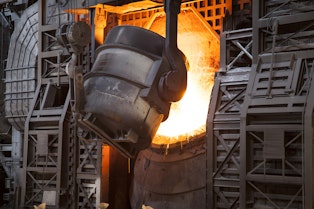
Steelmaking uses coking coal for heat and coke is also central to the chemical process of converting iron ore to elemental iron. Both processes produce carbon dioxide.
However, hydrogen can act as a fuel to provide heat and be the chemical reducing agent, getting rid of these emissions. In fact, all the major European steel players are currently building or already testing hydrogen-based steel production processes.
Alternatively, carbon capture and storage (CCS) has been mooted to remove emissions at the end of the process. However, not everyone is convinced by CCS’s efficacy. Finally, steel can be recycled without emissions, although demand is too large to be met with recycled metal alone.
Cutting emissions from cement
The manufacture of cement–which when mixed with aggregates such as sand or gravel produces concrete–is also a vexing problem for anyone with an interest in decarbonization.
Every 1,000 kilograms of cement emits 814 kilograms of carbon dioxide as limestone is ground down and heated to 1,450 degrees centigrade, to create calcium oxide.
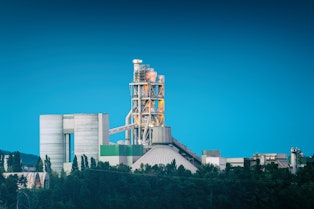
If you add the inevitable carbon costs of mining and transporting the raw materials, you end up with a figure of roughly one tonne of carbon emitted per tonne of cement produced.
Figures for this essential material’s global impact vary but tend to range up to around 10% of all emissions. But even figures at the low end, say around 3%, represent a significant slice of the carbon pie. Aside from using CCS, there are several potential solutions to this.
These include geopolymer cement, which uses fly-ash, blast-furnace slag, mine tailing and other industrially produced wastes as precursors.
The process occurs at much lower temperatures than that for conventional cement, and overall the geopolymer cement delivers up to an 80% reduction in CO₂ emissions.
Reaching net zero in plastics
Unlike steel and cement, the chemical industry uses carbon-carrying coal, natural gas and oil as its feedstock precursors.
So, depending on how the chemical is used or disposed of, creating the millions of chemicals that drive the modern world may have a net emissions benefit, locking up carbon molecules rather than releasing them into the atmosphere.
However, this is dependent on the energy driving the process being derived from renewable sources. One large stumbling block to the greening of the chemical industry is another vital feedstock precursor: hydrogen.
Right now, hydrogen is largely manufactured from natural gas and releases carbon dioxide as a by-product.
The green hopes for the steel industry also rest on hydrogen replacing hydrocarbons as a reducing agent, as well as using renewable electricity in the industrial process. Clearly, generating zero-carbon or ‘green’ hydrogen is an essential step in decarbonizing industry.
The promise of green hydrogen
The good news is it is possible—and has been so for at least 140 years. The electrolysis of water to produce hydrogen and oxygen is a tried-and-tested technique. But it is also one which makes strict demands of electricity supply.
Despite the increasing affordability of wind and solar, they remain intermittent sources of electricity. The challenge can be partially remedied with battery energy storage (BESS), a sector Pacific Green has a long-term commitment to.
An even better approach for green hydrogen production, where environmental conditions are right, is a low-carbon energy source with its own integrated energy storage function, which can provide dispatchable electricity long after the sun goes down.
Concentrated solar power (CSP) is a mature, proven renewable energy technology that can use molten salt to store multi-megawatt amounts of energy, with discharge times easily up to 12 or 15 hours a day.
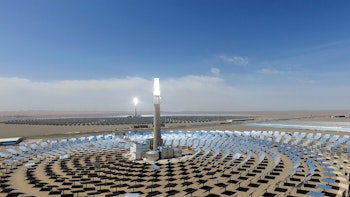
Our team has already developed, designed and engineered three utility-scale CSP operating reference plants in China with strategic partner Shouhang, including one 50 MW parabolic trough plant and two molten salt tower projects of 10 MW and 100 MW respectively.
As our development pipeline ramps up, investment in CSP also becomes a longer term bet on green hydrogen. CSP can also provide process heat for a range of industrial processes, making it a potentially valuable addition to industry hubs in high-irradiation areas of the world.
Joined-up thinking
More generally, the key to decarbonizing industries such as steelmaking, cement manufacturing and plastics will be to use a variety of technologies, tightly integrated to meet the needs of each sector.
This kind of joined-up thinking is somewhat new to the renewables sector but comes naturally to us a Pacific Green, since we have experience in industries as varied as shipping and water desalination.
We are keen to apply this knowledge to the cost-effective decarbonization of all industries and are looking to work with innovative industrial leaders on potential solutions.
Publish date: 26 July, 2022